While guitar isn’t as popular as it was in its heyday during the classic rock era, millions of people enjoy playing it today. But have you wondered how a guitar is made?
In the workshop of a luthier, the aroma of rosewood and mahogany pervades as the craftsman carefully selects the finest tonewoods for their acoustic properties and aesthetic appeal. These selected woods are skillfully shaped and contoured, a critical step for the final sound of the guitar.
The assembly of the guitar transcends the sum of its parts, creating an instrument of superior quality. The detailed fretwork and the application of the finishing polish are executed with precision, captivating those interested in the art of guitar-making.
Selecting Quality Materials
The construction of a guitar hinges on the selection of materials, where woods play a pivotal role in defining the instrument’s sound characteristics. East Indian and Brazilian rosewood, commonly used for the back and sides of a guitar, contribute to the instrument’s warmth and sonic depth. Alpine spruce, chosen for soundboards, is revered for its crisp sound and excellent resonance. Mahogany, a preferred material for necks, ensures durability and comfort in playability.
Electric guitars, while relying on electronic components for sound production, also benefit from quality construction. Their bodies, often crafted from woods like basswood, swamp ash, or mahogany, enhance visual appeal and improve sound sustain. Fingerboards constructed from ebony offer a durable and smooth interface for the player, while rosewood serves as a prevalent alternative, delivering a comparable tactile experience.
In the United States and beyond, the use of these materials in acoustic guitars guarantees that every strummed chord and plucked note is amplified by the instrument’s superior build.
Designing the Guitar Body
The soundboard, or top, forms the core of the guitar’s acoustic expression, with spruce being the wood of choice due to its exceptional resonant capabilities for acoustic guitars. This choice wood contributes to the instrument’s desired sonorous quality. The incorporation of arched designs in both the top and back augments the guitar’s structural stability and enhances its sound.
In electric guitar construction, the integration of electronic components into the body is executed with exactitude. The strategic placement of pickups and controls is essential for the accurate translation and modulation of string vibrations.
The final step involves the careful shaping and smoothing of each part, followed by their assembly using adhesive. This process culminates in the creation of the guitar’s resonant chamber, the origin of its distinctive tone.
Crafting the Neck and Fretboard
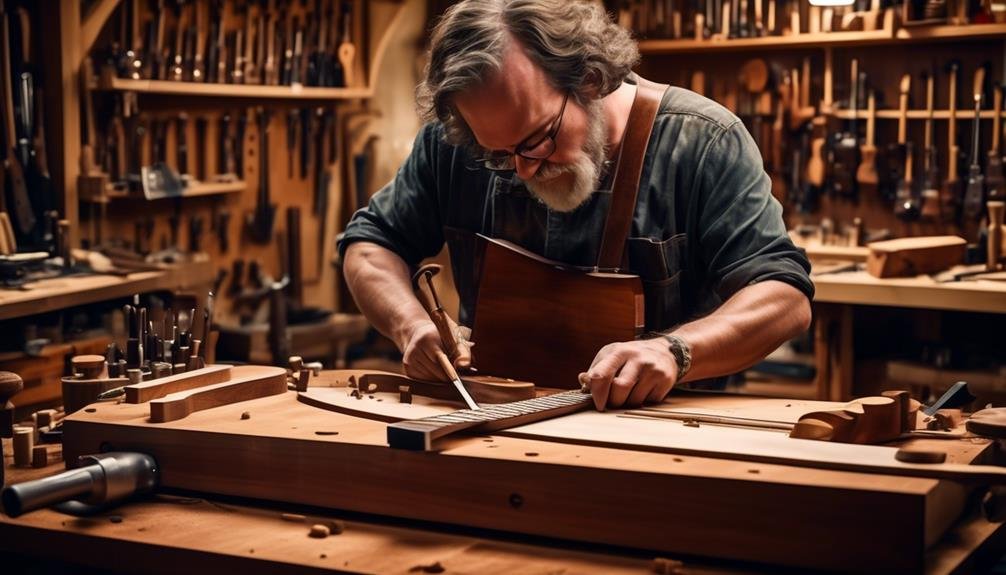
Luthiers select mahogany for neck strength and rosewood or ebony for fingerboard smoothness. The neck, crafted from a single wood piece, incorporates a truss rod for stability against string tension. This rod is inserted into a neck channel before the neck is glued to the fingerboard.
Rosewood or ebony compose the fingerboard, providing durability and a smooth touch. Fret slots are precisely cut into the fingerboard to hold the metal frets.
The 20 to 24 metal frets, secured and hammered to the correct height, enable clear and true note production. The completed neck and fretboard assembly is meticulously joined to the guitar body, allowing the instrument to produce music.
Assembling the Components
Luthiers join the neck to the guitar body using a dovetail joint, which reinforces structural integrity and sound resonance. Precision is crucial in assembling the guitar’s body and neck, often employing glue or bolt-on techniques for stability.
The soundboard, alongside the back and sides, receives careful consideration. The bridge, chosen for its quality, is positioned with precision for optimal string height and sound. The fingerboard is prepared to be smooth for the strings.
The final assembly includes mounting the tuning machine on the head’s back, enabling precise tuning. The Pleking process follows, where a machine adjusts the frets to the ideal height for clear, in-tune notes once the strings are attached.
Finishing and Detail Work
In the final stages of guitar creation, craftsmen meticulously smooth the guitar neck and body by hand to ensure comfort and playability.
The next step involves attaching the fretboard and embedding steel frets into the designated grooves.
After securing the neck to the guitar body and installing the saddle and bridge, the instrument is prepared for coating applications.
An undercoat is applied first, followed by the chosen paint color. This is then sealed with a layer of polyurethane resin.
These coatings serve multiple purposes, enhancing the guitar’s visual appeal, contributing to its acoustic properties, and protecting it from environmental fluctuations.
For electric guitars, creating recesses for the electronic components is a crucial finishing step.
Craftsmen carefully route the underside of the guitar top to accommodate wiring and circuit boards, ensuring the instrument’s structural integrity is maintained.
Areas prone to damage are fortified to endure the tension of the strings and regular handling.
Quality Assurance and Testing
Before reaching the customer, each guitar endures a comprehensive quality assurance and testing phase, ensuring its superior aesthetic appeal, excellent sound, and smooth playability. Craftsmen construct guitars with attention to detail, utilizing mahogany for the body due to its sound-enhancing resonance and resistance to string-induced distortion. Rosewood, known for its longevity and rich sound, is the preferred material for fretboards.
The durability of the strings, capable of handling high tension, is thoroughly examined. The guitar’s tuning stability and sound consistency are critically evaluated. Teams conduct stress tests and simulations, verifying the instrument’s capacity to withstand regular usage.
Visual examinations are essential to identify any aesthetic flaws, upholding the highest construction standards. Technicians, adept in assessing instrument quality, test each guitar for comfortable action, straight neck alignment, and the reliability of electronics.
The customer’s first strum reflects the instrument’s embodiment of expert craftsmanship and rigorous quality oversight.